The key to success for any mechanism is the concerted operation of all its elements. With this in mind, rig equipment that works efficiently and interruption-free is one of the most important factors in productive well construction. Proper equipment service and maintenance reduces the risk of accidents and results in a safer environment for rig personnel.
One of the key ways to ensure uninterrupted equipment performance is periodic maintenance as per the manufacturer’s recommendations. This service includes quarterly, semi-annual, and annual maintenance, plus five-year inspections and major repairs. Periodic service plays a significant role in the estimated life of consumable spare parts, which the equipment manufacturer uses to create a list of the necessary spare parts and materials for replacement or monitor the tolerance parameters. Timely replacement of these parts and materials helps avoid premature wear of other units and components. Another important factor to consider is that, in most cases, equipment operation occurs under excessive loads and it is, therefore, necessary to perform periodic maintenance more frequently.
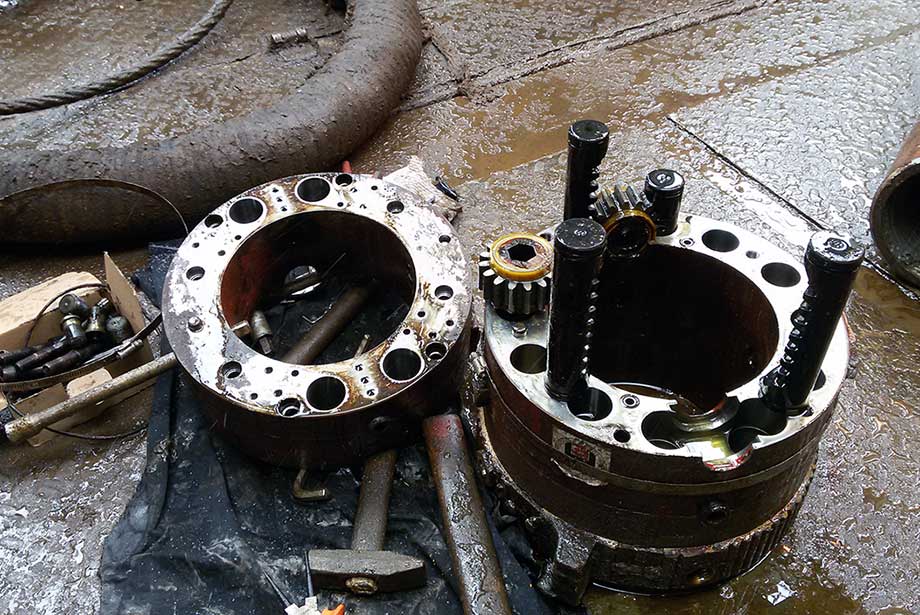
EQUIPMENT
Using unreliable diagnostic equipment during inspections and servicing leads to errors and lost time, ultimately lowering the quality of the work.
Our company uses certified measuring and diagnostic equipment from leading world manufacturers. Mobile run-in stands, repair containers and diagnostic complexes allow us to perform a wide range of operations directly on-site. We can run diagnostics and perform run-in activities without transporting equipment to repair bases, saving the client time and funds.
Оборудование с которым мы работаем
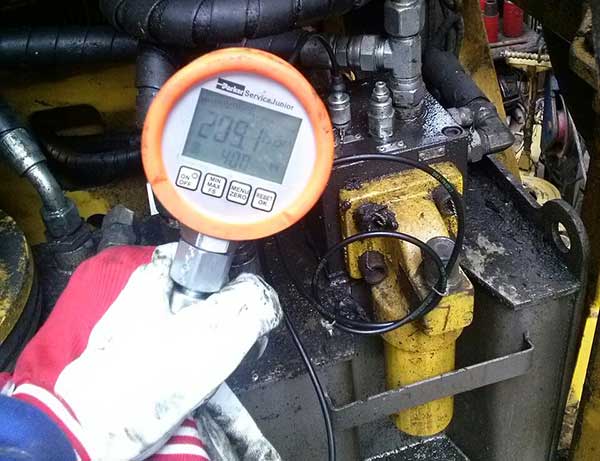
Использование ненадежного диагностического оборудования при поиске неисправностей и оказании сервисных услуг, приводит ошибкам, потере времени, снижению качества выполнения ремонтных работ.
Наша компания использует поверенное измерительное и диагностическое оборудование ведущих мировых производителей. Мобильные обкаточные стенды, ремонтные контейнеры и диагностические комплексы позволяют выполнять широкий перечень работ на объекте эксплуатации оборудования. Возможность выполнения диагностических и обкаточных мероприятий без транспортировки на ремонтные базы позволяет сэкономить время и средства Клиентов.
STAGES OF COOPERATION
