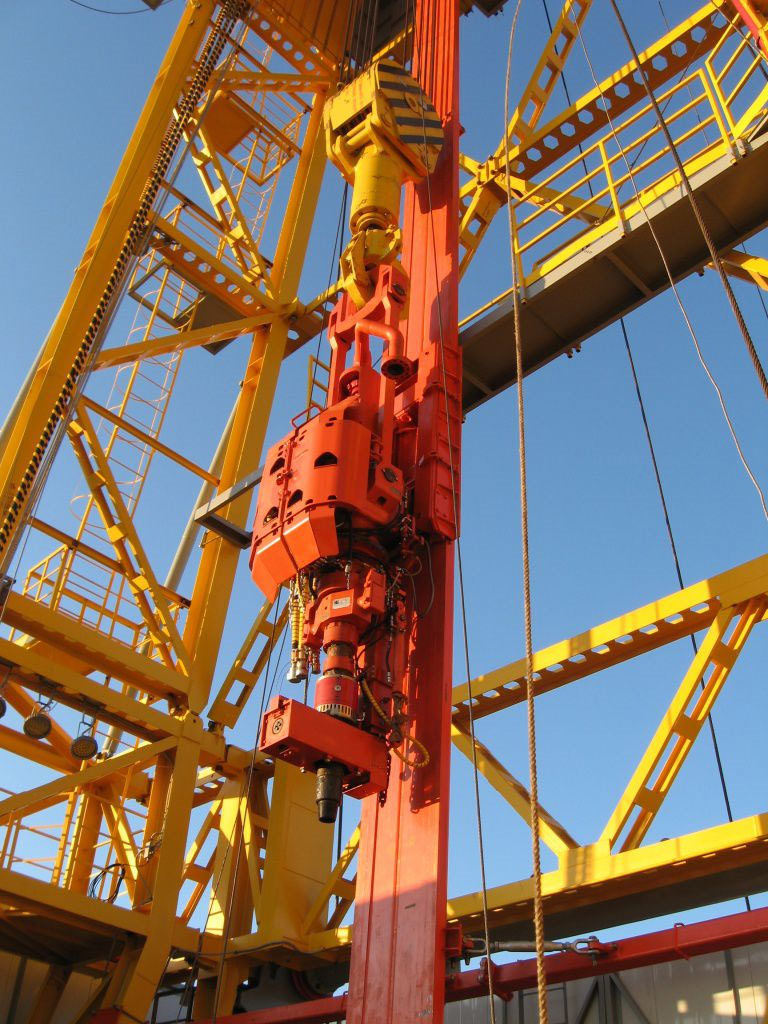
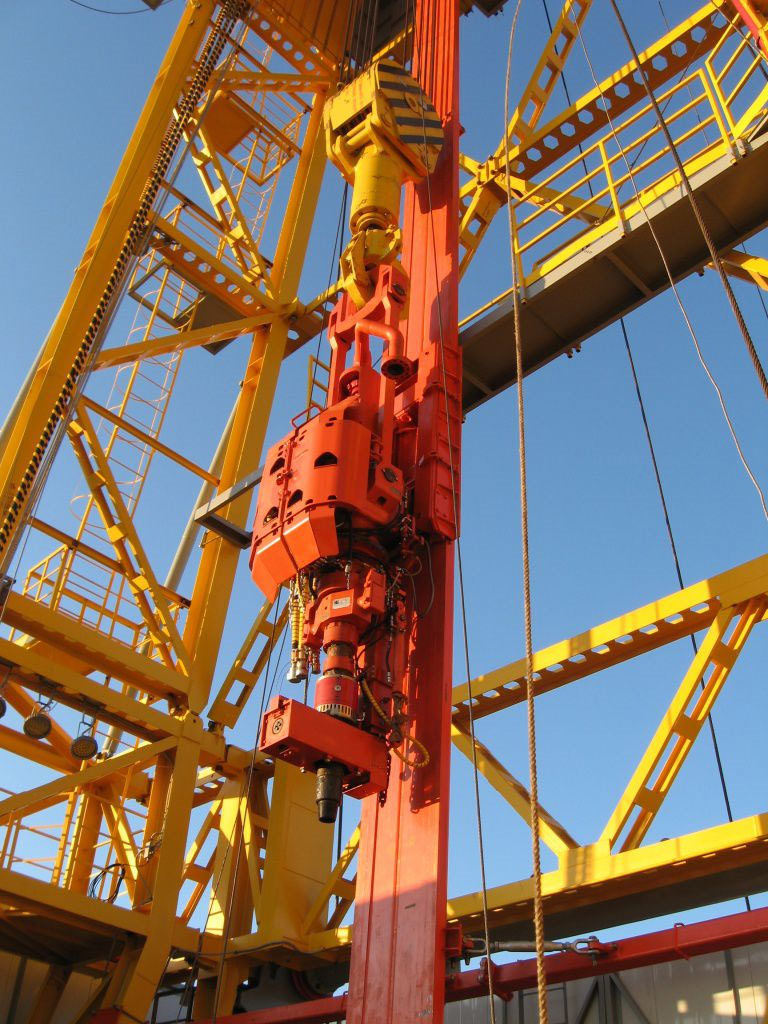
Despite of the fact that TDS (top drive system) was developed in the early 1980s, in Russia TDS became popular not for a long time ago. The demand for this equipment arose near 5 years ago. Top drive system is a multi-operated system that can simplify drilling rig service operation for operating staff. It is widely used with different types of drilling: vertical, directional and horizontal.
With the TDS using the majority of drilling rig operation processes can be mechanized and replace the major part of manual labour while making a connection, developing borehole, enlarging borehole and lowering the casing. The automatic control of operation process can control torque data and pressure on the bit.
TDS operating principle
TDS is fixing with the wire rope to the drilling rig hoist and can toss. TDS consists of swivel and one or more electric or hydraulic engines. The top part of derrick drive has threading thrust chamber that can automatically bring out the drilling pipe threading portion from the clutch while making a connection or derrick dismantling are processing. The thread damage is absolutely excluded.
Making a connection or derrick dismantling are performed with the help of manipulator that can turn drilling pipe to the proper direction. This manipulator is provided with the gripper which is intended for pipe clutch fixing while making-up of joints.
The advantage of TDS
The technology of TDS can essentially cut time while making a connection, it mitigates the risk of workover bit sticking and simplify casing tube passing with the help of turning through inaccessible areas. The top part of the drilling rig can be installed pretty much at any time, not stopping the drilling process. TSD system can replace the large part of manual labour compared with traditional technologies. The TDS system simplifies the operation staff work, also essentially increases the operation process safety.