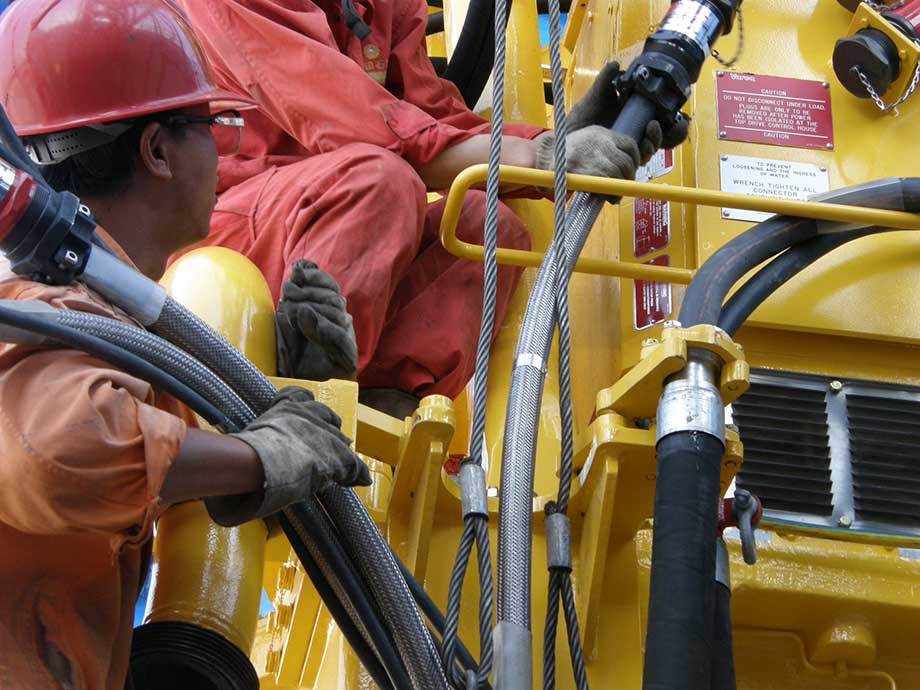
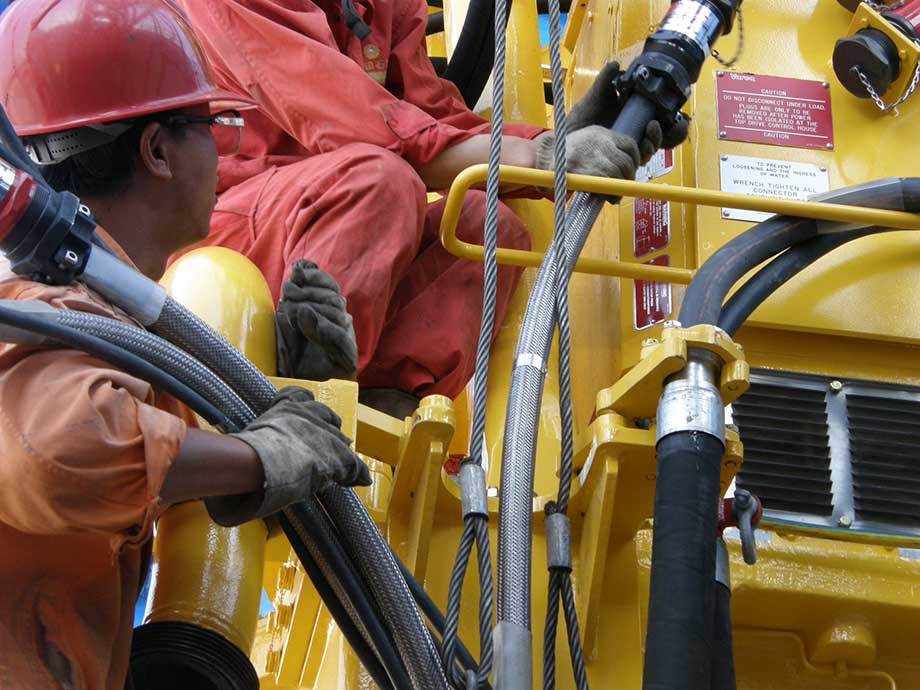
Oil Link, Ltd. offers service, maintenance, repair and spare parts for the top drive systems of leading American, European and Chinese manufacturers.
The top drive system (TDS) has recently become the most popular method of drilling oil and gas wells. Both imported and domestic rigs are equipped with this system, which is a fundamentally new type of drilling rig mechanism that performs a number of technical operations. A top drive is a drill head with a swivel, equipped with a mechanization system for tripping. TDS drilling rigs are widely used across the world.
TDS performs:
- Drill string rotation while drilling, exploring and expanding the wellbore
- Screwing and fastening of drill pipes
- Tripping, including the pipe stand connection, and casing-lowering operations
- Drill string rotation when drilling with a bottom-hole motor
- Well washing and drill string rotation during tripping;
- Drill string reciprocating and washing during accident and complication elimination
Top Drive Service Support
When moving to the TDS site, our specialists perform a full range of operations to ensure the top drive works reliably, safely and economically.
Our service engineers resolve key issues in the provision of integrated solutions that eliminate downtime and time lost during drilling and equipment operation, as well as increase TDS efficiency during installment at the drilling rig.
To this end, our representatives:
- Train company employees
- Remain a constant presence in the field for the top drive’s entire period of operation
- Supervise initial and repeated installations as well as the equipment disassembly
- Perform commissioning and adjustment operations, independently or with the client’s company employees
- Provide technical support and monitor the process of proper and safe TDS operation
- Execute top drive maintenance regime, which includes routine maintenance and preventive maintenance in the field
- Inspect the TDS periodically and annually, monitoring the system’s status to avoid unforeseen accidents
- Complete comprehensive inspections of equipment on Oil Link’s production bases, subsequently registering the conclusion and issuing the quality certificate
- Provide top drives with original spare parts, consumables and the necessary equipment
- Provide the client with reports on the TDS status and make recommendations on its maintenance and use
- Take the necessary measurements and collect information about the operation of our top drives for further study and information compilation to improve the quality and performance of our equipment
Supplying original spare parts, consumables and equipment includes:
- Supplying the well directly with the required number of spare parts and consumables to avoid downtime
- Reserving a single volume of spare parts and consumables at our production site for operational replenishment
- Manufacturing and providing safe drill pipe sub-drums
- Reserving and supplying the well directly with the 1st spare ball valve with one repair kit
- Reserving an additional ball valve with one repair kit at our production site for the client
- Promptly replenishing the reserve of spare parts and components at the production site during the order fulfillment stage
Servicing a TDS
Technical diagnostics and maintenance of top drives include:
- Dismantling the parts planned for diagnostics
- Cleaning and preparing parts for diagnostics
- Providing technical support for nondestructive testing of the bearing and parts operating under the load of the main components
- Creating an engineering report and defect list for the TDS
- Maintaining materials and assist in eliminating defects identified during the inspection
- Completing cleaning, painting, and installation
- Performing operational tests (commissioning)
- Offering recommendations on the creation of a consignment warehouse for the necessary spare parts for regular operation
Rig equipment requires routine inspections and preventative maintenance at
3 months
Duration: 4 working days
Required personnel: 1 mechanic, 3 workers
6 months
Duration: 6 working days
Required personnel: 1 technician, 3 workers
1 year
Duration: 16 working days
Required personnel: 2 mechanics, 1 electrician
Required equipment: Restricted area, 25-ton overhead crane
If possible: paint shop, shotblasting, access to a mechanical workshop with lathes and a welding shop. Non-destructive testing is performed according to the recommendations of our specialist.
TDS Technical Maintenance During Drilling
- Preparation and analysis of a daily, weekly, monthly checklist to determine the performance dynamics of the equipment
- Daily, weekly, and monthly maintenance
- Reporting on daily, weekly, and monthly maintenance
- Ensuring the necessary conditions for optimal TDS operation
TDS Advantages
Saves time on pipe extension when drilling
Extending the column with a 28-meter drill pipe string eliminates the need for every two out of three drill pipe joints.
Reduces the likelihood of the drilling tool sticking
The power swivel allows us to connect to the drill string to restore its rotation and circulation of the drilling fluid at any time while the elevator is lowering or lifting the tool for 2-3 minutes, thereby preventing the tool from sticking.
Expands (reams) the wellbore when lowering and lifting the tool
Increases accuracy of well drilling in directional drilling
The candle can be held at a predetermined position along the entire length of the pipe stand when using a deflector with a hydraulic downhole motor to measure the well angle, which leads to a better column orientation and fewer control surveys.
Improves safety for the drilling crew
The ability to build a candle, rather than a single tube, reduces the number of connections, which reduces the likelihood of accidents.
Reduces the likelihood of fluid ejection from the well through the drill string
Using a mechanized, dual ball valve (preventer) allows you to close the column’s internal hole quickly, preventing spillage of drilling mud when detaching the power swivel barrel from the pipe stand. The driller carries out the entire operation, with no need for other members of the drilling crew to participate.
Facilitates casing pipe lowering in areas where drilling creates complications
With TDS, we have the ability to run the casing string with rotation and rinsing by adding a special casing pipe sub.
Improves the core quality
Drilling the entire length of the pipe stand without a single-pipe extension improves the core quality and reduces the number of runs.
Ensures accurate torque when screwing and threading
Using a DC motor or an AC motor with a variable frequency makes it possible to get an accurate, smooth variable torque attachment for each connection, which increases the drill pipe’s service life.
The top drive
- Captures the pipe (pipe string) for lifting
- Captures the pipe (pipe string) for screwing (unscrewing)
- Screws (unscrews) the threaded pipe joints
- Connects to the pressure line (trunk) to flush (clean) the well
- Drills (drill string)
- Lays pipe
Description of TDS Construction
The movable part of the TDS consists of a swivel reducer, which is suspended on the traveling block clevis bails.
An explosion-proof DC motor is mounted on the top cover of the swivel reducer. One end of the motor shaft is connected through the elastic coupling to the high-speed shaft of the reducer and, on the other end, there is a disc brake. The frame fastens to the swivel reducer housing, through which the roller block transfers torque to the guides and then to the derrick. Between the traveling block and swivel reducer, there is a thread unloading system that automatically withdraws the threaded section of the drill pipe lock nipple from the coupling during unscrewing and ensures the stroke of the nipple while screwing the lock. This prevents damage to the threads.
A pipe manipulator, fed by a gear pair driven by a hydraulic motor, can deploy the elevator in the desired direction: to walkways, pipe joints or in any other direction as needed.
A tube clamp grips and holds the rotation of the upper pipe clutch while screwing or unscrewing the swivel stem.
A manual ball valve is screwed between the nipple and the swivel barrel for routine sealing of the inner swivel barrel hole. To effectively close the swivel barrel hole, an internal preventer (double ball valve) is installed before the tap, which simultaneously retains the rinsing fluid residue after unscrewing the drill string.
The swivel head transfers the working fluid from the non-rotating part to the rotating part of the top drive system and prevents the hydraulic lines from disconnecting when the pipe manipulator rotates with the drill string during drilling, working the well or positioning the elevator deflector sheaves.
A tilt system is designed for tapping and bringing the elevator to the center of the well. This system consists of bails suspended on the lateral horns of the traverse. The tilt system’s hydraulic cylinders are attached to the bails.
The central feature of the TDS is the ability to mount it at any point during drilling with virtually no interruption.